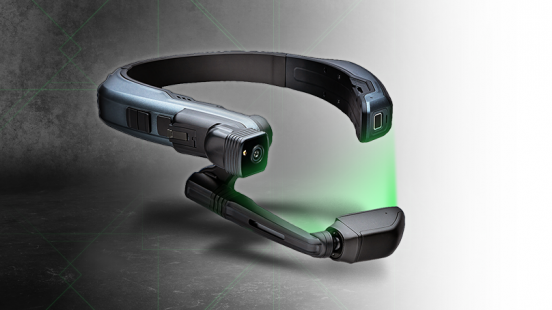
Unexpected challenges often become the driving force behind the implementation of new technologies. This was also the case for our client – AN-ELEC.
Faced with logistical difficulties caused by the pandemic, it became necessary to find a solution that would streamline the process of remote acceptance inspections. The answer to these needs turned out to be augmented reality (AR).
Importantly, its implementation not only helped overcome short-term issues caused by pandemic restrictions but also continues to effectively support daily operational processes.
Client
AN-ELEC Sp. z o.o. is a company specializing in electrical and locksmith services, operating in both the marine and land-based industries. It offers comprehensive services including design, construction, modernization, implementation, maintenance, and servicing of electrical installations.
Challenge
In 2020, AN-ELEC was faced with the need to carry out remote acceptance inspections of switchboards for a Dutch client. The pandemic made it impossible for the client to travel to Poland, and traditional quality verification methods required physical presence. The initial approach—using conference cameras in the workshop—was acceptable but involved a high time investment and the engagement of multiple company departments.
Solution
AN-ELEC decided to implement the RealWear Navigator 520 assisted reality headset with a FLIR thermal camera. A key element of the solution was the TeamViewer Frontline xAssist software, which enabled real-time visual support and interactive annotations. This allowed experts to place instructions directly on the screen, making it easier for on-site workers to understand and carry out tasks. Additionally, functions such as photo capture and video recording—which can be attached to the session summary report—proved extremely useful for later analysis and training.
The integration was handled by Arsys, a company specializing in solutions for industry and manufacturing businesses.
Result
The implemented solution allowed AN-ELEC to significantly improve the efficiency of the acceptance process. Technical preparation time was reduced, involvement of multiple departments was minimized, and high-quality audio and video transmission was ensured—even in noisy industrial environments. Thanks to features such as image capture and session recording, AN-ELEC can now better document and analyze the acceptance process, leading to improved customer service quality.
How much can AR simplify processes in your company?
Let’s find out.
Contact me and tell me about your challenges related to efficiency, logistics, or workplace safety. Together, we’ll estimate how augmented reality can support you in these areas.
+48 663-005-108
mariusz.rozbicki@elmark.com.pl